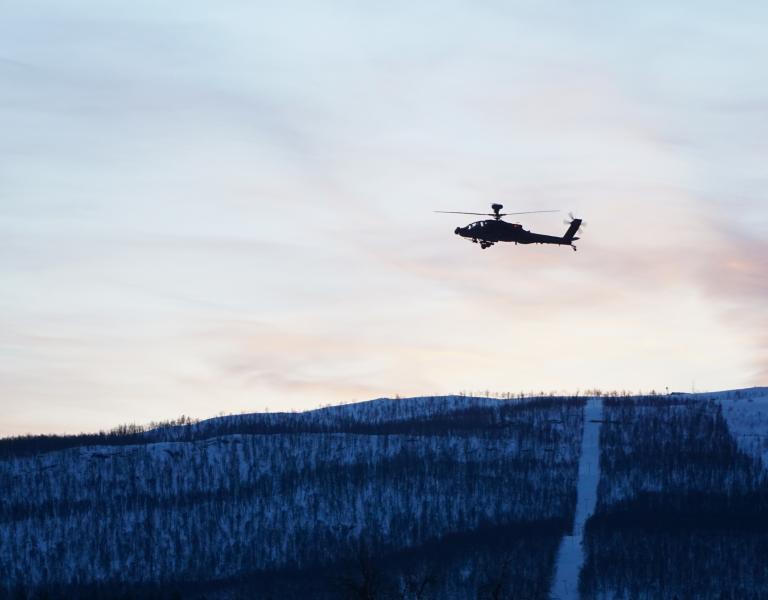
Heli One - Maintenance Solution Analysis
Helicopter support solution designed for highest operational availability and low cost.
Systecon assisted Heli-One, one of the world's largest helicopter maintenance companies, analyze parts of the maintenance solution for a type of helicopter. The purpose of the project was to identify the optimal distribution of spare part and replacement unit inventory levels to ensure maximum operational availability for the Sikorsky 92 helicopter at the lowest cost.
In short, Heli-One wanted help with the following:
- Obtain recommendations for the optimal distribution of replacement units to achieve a fixed helicopter availability at the lowest cost
- Enable calculations of helicopter support costs and advance quotes to potential customers
- Display the effects of various improvements and changes in the supply chain
To answer the questions above, the situation was modeled with OPUS10, using the following assumptions:
- 17 helicopters allocated across the bases, see figure
- 197 different replacement units
- 9 different helicopter bases, 3 repair shops, 1 centralized inventory
- A specific number of flight hours planned per year and base
- Transport times, see figure
The helicopter bases are supplied from the central inventory in Amsterdam, which also operates as a hub for replacement units sent between the bases and the repair shops. There were two groups of bases with lateral support, one group in Norway and one group in Great Britain. The bases in each group could supply each other with replacement units if available, when needed.
Systecon and OPUS10 calculated that the optimal distribution of the replacement units would result in an annual support cost of X million dollars, if the total helicopter availability was set to 95%. The OPUS10 result also included a proposal for purchasing a certain number of the 197 replacement units, and how to allocate them within the organization. The OPUS graph provides a direct answer to the question of how the helicopter availability is affected by how much is invested in the replacement units, assuming approval of the optimal replacement unit allocation proposed by OPUS10.
Additional OPUS10 analysis showed that the support cost would not be impacted by moving the inventory from Amsterdam to Bergen. On the other hand, investing in superior-quality components for the 20 components with the highest failure rate saved a relatively large amount of money. Systecon also provided a proposal showing the benefits of minimizing the repair time for certain components – a proposal that resulted in additional reductions of the annual support costs.
The Heli-One Project is a good example of how Systecon, using its own modeling expertise and tools, can provide powerful analytical data for those who own, manage or maintain equipment and supply systems. Designing maintenance solutions using a clear and traceable relationship between operational availability and total costs involves many difficult tradeoffs between investments in different parts of the system or support systems. OPUS10 and Systecon's other software applications can be a great help when analyzing which investments are most useful. Implementing the measures proposed by the analysis results in the optimal balance between investment and allocation of spare parts, investment in repair shops, and supply chain design. This increases the operational availability of the equipment and supply system, while reducing the inventory cost.
Book a demo
Related Articles