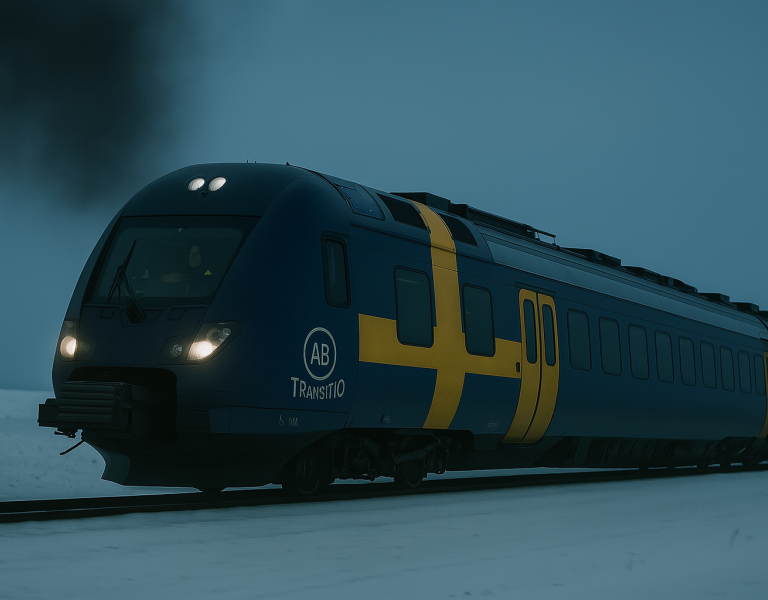
Resource dimensioning that supports efficient railway traffic
Do we have the right maintenance strategy? Will our current depot capacity be sufficient? Do we have enough vehicles to meet our timetable? These are important challenges. A poor basis for decision-making increases the risk that short-term or no decisions are made. For the business and passengers, the results are obvious.
Do we have the right maintenance strategy? Will our current depot capacity be sufficient? Do we have enough vehicles to meet our timetable? These are important challenges. A poor basis for decision-making increases the risk that short-term or no decisions are made. For the business and passengers, the results are obvious.
Planning and operating a railway is a complex task involving many interacting variables that affect the quality of operation and costs. It includes various types of vehicular characteristics, preventive and corrective maintenance, failure rates, spare parts supply, the number of depots and their designs including lifts, wheel lathes and other maintenance equipment, among others. Faced with changes in operations, such as the purchase of new trains or the reconstruction of a depot, there’s a great need to assess the impact on the overall system. However, it’s difficult to know how one factor affects other factors. It’s also difficult to predict how the changes impact on operations and vehicles’ total life cycle cost. In many cases, this uncertainty leads to making short-term decisions or no decision at all, with negative results for the business. The more complex the whole system is the harder it is to make the right decision.
Using Opus Suite, capacity analysis and resource dimensioning aims to create optimal conditions over time for a system to be able to perform at the required level while reducing life cycle costs as low as possible. In one model, the technical system, (i.e., the train), its operation and the supporting maintenance organization can be studied simultaneously. This makes it possible to find the optimal trade-offs for how resources should be sized and where they should be placed to provide the best overall effect. You can also see how changes in, for example, various sub- elements influence each other, minimizing the risk of costly sub-optimization.
Depot capacity analysis
In a depot capacity analysis, a model of the traffic you want to study is created. The model includes detailed information on vehicles (number of trains and its structure, maintenance schedules, failure rates), the current operating profile (the desired traffic) as well as the maintenance organization (depot, working tracks, hoists, tools, staff and opening hours). Subsequently, the system's operation and resource needs are simulated, hour by hour, for the coming years. It is not uncommon to have an analysis period of 10 to 20 years. The simulation is performed with random variations in, for example, critical faults on vehicles, broken lifts, or collisions with animals. A large number of simulations provide results presented in the form of a mean and a spread with confidence intervals, making it possible to assess uncertainties and risks. The results show, among other things, the utilization rate of various maintenance resources in the depot and how accessible the vehicles used for transport will be. Using the results, current and future bottlenecks in the system are identified, and measures to eliminate these are proposed.
Analyses with simulation software SIMLOX is especially powerful when you have several alternative operating and maintenance solutions to choose from. It is difficult to know which of these best meet the requirements and how traffic is affected by various factors. For example, one can assess whether the existing depot can handle the increased maintenance needs that a proposed increase in traffic entails.
Examples of performed analyses
Commuter train services in Stockholm is expected to increase in the coming decades and huge investments have been made and will be made in depots and new trains. As the new trains are delivered, the old trains will be phased out and existing depots must be adapted to maintain the new trains. All of this must take place while maintaining high vehicle availability. To make the right decisions in their depot redevelopment projects SL has hired Systecon to perform depot capacity analysis.
The results of the analyses have included giving clear answers to when and how the tracks in the depots need to be adapted so that they can continue to maintain all types of vehicles with high efficiency, without critical bottlenecks occurring. This analysis would be practically impossible to implement without a simulation tool like SIMLOX, in which vehicles, traffic and maintenance organization can be analysed in the same model, and where changes over time can be studied.
There are other examples of depot capacity issues that could be studied by simulation. For example, depot opening hours and staffing at different times of the day, the effects of changes in the structure of the maintenance plan and the closure of a depot in connection with engineering works.
Spare parts optimization
Spare parts optimization creates a model to describe the vehicle, its component parts and replacement units as well as the maintenance organization to supply the vehicles with spare parts. Thereafter, the spare parts need is optimized against system availability and cost. The result is the so-called OPUS curve where each level of availability (e.g., 98 percent) receives an optimal proposal for a range of spare parts and a location in the organization where the spare parts are kept in stock (i.e. the optimal distribution of spare parts that provide maximum availability per euro).
With Systecon's software OPUS10 optimized spare parts inventories for individual or multiple technical systems are performed simultaneously. The optimization can be made both in connection with the initial acquisition of a new fleet, at the commissioning of a new fleet, or to adjust an existing business to either improve access or reduce costs. An optimization with OPUS10 usually provides substantial savings in the capital that is tied up in spare parts by storing the correct items, in the correct quantity, at the correct location.
Examples of performed analyses
A vehicle owner had ordered a large number of new vehicles and the supplier had recommended the customer to buy a certain number of 50 different so-called high value components for its stock of spare parts. The vehicle owner was unsure if the proposed parts list was optimal. Systecon was hired, and an OPUS10 analyse of the proposed parts list was performed. The results of the analysis showed that it was possible for the customer to order fewer components than proposed by the vehicle supplier and still maintain the same availability of the vehicles. Another option was that for the same total cost to select a different distribution of spare parts and achieve a considerably higher availability of vehicles. This analysis would be practically impossible without an optimization tool like OPUS10.
Summary
Capacity analysis and resource optimization analysis tools in Opus Suite make it possible to analyse the technical system, its operation and the supporting maintenance organization and balance them so that the operator can provide the planned service at the lowest possible cost. To ensure the overall benefit to the entire transport, all these three dimensions need to be considered together. The analytical result should be an integrated part of the decision-making process when changes in the operations are planned or cost savings in the operation are desired.
At Systecon we have extensive experience in implementing this type of analysis assignment for clients in the railway industry as well as in other industries. We have a comprehensive approach and, together with the customer, we build a model that reflects the customer's operations and decision-making situation. An analysis project doesn’t need to be particularly extensive. Once a basic model is created it's easy to refine this gradually and address a variety of questions that arise.
Would you like to know more?
Our offers in railway
Resource dimensioning
Reference project: SL – Depot dimensioning