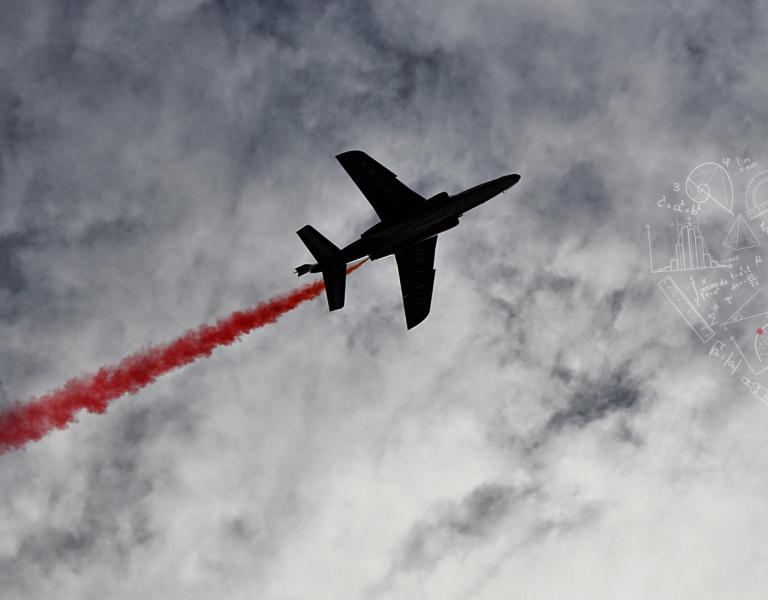
SAS - Spares for Multiple Service Level Agreements in Airline Operations
The investments in spares were significantly lowered thanks to system-based spares optimization.
Running an airline is unavoidably expensive and many airlines operate with low margins. An airline can trim operating expenses in many different ways. The potential for savings is usually great in the costly area of supply of spare parts.
At the time of this project, the company now known as ST Aerospace Solutions Europe, was SAS Component, a separate business unit within Scandinavian Airlines Systems Group. SAS Component offered repair services and supply of rotables to SAS and other airline operators in accordance with service level agreements. This included management of the customer's inventory of rotable components. This type of pooling-arrangement facilitates cost effective support of the aircraft with the objective to minimize downtime due to maintenance and repair.
SAS Component supported its customers from a network of airports with three main bases in Copenhagen, Stockholm and Oslo. At the time of this study, each of the main bases was responsible for managing and repairing certain components, so the support structure varied for different items.
SAS Component experienced very slow inventory turnover and a high share of slow/non-movers. The default mode of transportation was by truck, but there were thousands of emergency shipments by air each year in order to meet the agreed service levels.
SAS Component wanted to evaluate the potential benefits of using a more advanced tool for spare parts optimization. Systecon was therefore asked to perform a study to:
- Determine and evaluate current status – What theoretical service levels were possible, considering the current investment, inventory, and allocation?
- Estimate savings potentials if using OPUS10 – What would be the optimal spare parts investment if completely new provisioning were to be implemented?
- Suggest changes for short-term improvement to increase service levels.
- Determine requirements for direct data transfers to facilitate easy import and export of data to OPUS10 from existing ERP and legacy systems.
Major results from the project:
- The existing solution resulted in a service level of 92.8% to be compared with required 95%. Furthermore, all customers except SAS experienced service levels below 90%. However, the customer never experienced this since shortages were handled by emergency shipments, which were very costly for SAS Component.
- Using OPUS10 optimization, and assuming that all provisioning could be done from scratch, with no current inventory, a new solution could meet the overall target service level with a 33.5% lower investment in inventory.
- The overall target service level could be met by just reallocating current stock in an optimal way.
- Furthermore, with a relatively small additional investment the service level could be increased significantly, providing a more robust solution.
A hypothetical case provided examples of how OPUS10 can be used in negotiations with customers by quickly calculating:
- What additional inventory must be purchased to meet the demand of a new contract?
- How would adding the new customer’s existing stock to the pool affect the overall service level?
- How does a customer’s demand for a minimum local inventory of expensive items affect the costs for SAS Component?
Our analysis showed that SAS Component had done a good job with their previous methods for spare parts calculations but that the potential for improvements was still great. Improved results could be achieved with 33.5% lower investment. As a consequence of the project, SAS Component invested in the Systecon’s OPUS10 tool, which then became the standard for optimizing their spare parts inventory.
Book a demo
Related Articles