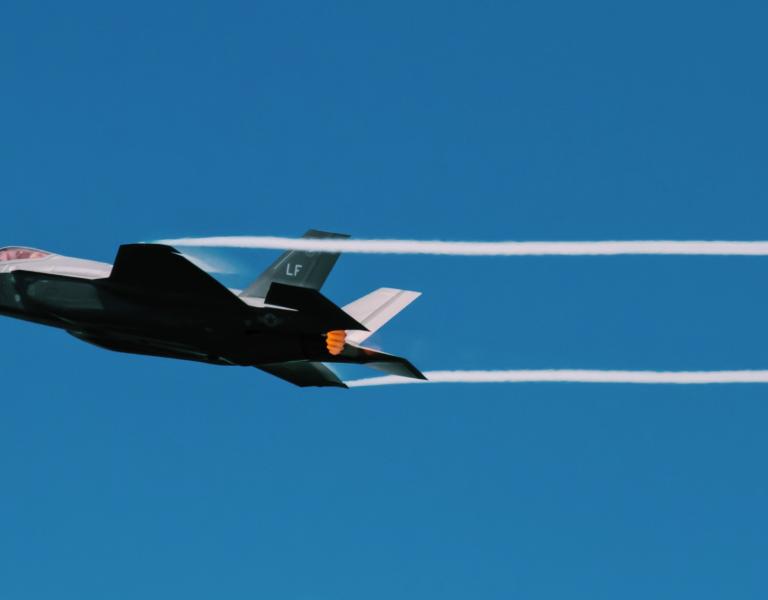
Systecon takes LORA (Level of Repair Analysis) to the next level
Level of Repair Analysis (LORA) is a method of analysis used to determine where to repair each component in a system, and whether it is more cost effective to discard an item rather than attempt to repair it. For a large system over many years, significant cost savings can be realized if the right decisions are made.
Level of Repair Analysis (LORA) is a method of analysis used to determine where to repair each component in a system and whether it is more cost-effective to discard an item rather than attempt to repair it. For a large system over many years, significant cost savings can be realized if the right repair decisions are made.
A number of years ago, Systecon introduced an entirely new way of approaching LORA by optimizing the entire logistics solution simultaneously at both an operational and organizational level. Now, we introduce an enhanced LORA-XT module—one of the big news in the next version of Opus Suite. For example, the LORA process may reveal that replacing a component involves a real repair cost that is hundreds of times greater than the purchase price when all costs are considered (maintenance staff, diagnostic equipment, inventory, shipping, etc.). If this item is replaced frequently over the course of many years, this presents an opportunity to save money by adjusting the repair process to generate economies of scale (improve reliability, repair and maintenance facilities, component repair, etc.).
Using LORA, a complete system support solution can be developed. It determines where to perform the required maintenance, what resources must be available to perform the maintenance, and what type of support the logistics infrastructure must be capable of delivering throughout the operational life of the system. It also considers repair levels, including i-level maintenance, where i-level maintenance occurs to optimize repair strategies. For this reason, LORA is one of the most important types of analysis performed prior to the introduction of a new system. For instance, the method is prescribed by the United States Department of Defense, and naturally, this is one of the reasons we are focusing on enhancing the LORA-XT functionality in Opus Suite.
Much has been written about the LORA methodology, and a lot of it is accessible on the Internet. The old American standard, MIL-STD-1390, is still a living reference document, even though the standard as such was canceled back in 1997. The Aerospace and Defence Industries Association of Europe (ASD) is conducting some standardization work, and the classic LORA methodology is described in some detail in their specification 3000L for Logistic Support Analysis. Systecon recently assisted Saab in preparing a corporate manual to support Saab's various business units in customizing the LORA methodology for each individual project.
One major limitation of the traditional LORA methodology, which has been used in developing maintenance strategies for a long time, is that it is based on considering one component at a time. This approach can work well when implementing a smaller system within an existing large, symmetrical organization. However, when implementing an entirely new major system, such as a new aircraft fleet, a new series of ships, or a new fleet of vehicles, or when the maintenance needs of the organization arise quite asymmetrically, there is a substantial risk of locking in suboptimal solutions. Only being able to see individual components one at a time with no overall assessment also means that it is difficult to predict how different decisions will work together and impact the overall life cycle costs. With a new aircraft fleet, for instance, what's best for the engine may not be what's best for the whole aircraft or aircraft fleet.
For this reason, Systecon introduced an entirely new way of approaching LORA by optimizing the entire logistics solution simultaneously. Instead of starting with each individual component and its maintenance needs, we started at the other end—how much flight time does the airline want, and at what cost? Instead of making a large number of sequential calculations, Opus Suite reviews all possible solutions simultaneously to identify cost-effective repair options and calculate optimal solutions based on all available information. What is the most efficient intermediate-level maintenance strategy for different components? Where should repairs take place? How many spare parts of each type are necessary, and what other maintenance management resources are required to maximize a given budget? This more advanced approach led us to develop LORA-XT, redefining the "L" from "Level" to "Location."
However, the current version of LORA-XT has certain constraints. For example, optimization is limited to primary components—those replaced directly within the complex engineering system. For components at lower indenture levels, the logistics solution must be explicitly defined. Additionally, the optimization does not yet incorporate intermediate level maintenance or preventative maintenance considerations.
Since more of our clients have switched to the LORA-XT module lately, we have been asked whether the current restrictions can be eliminated. This is the main reason why a new, more sophisticated LORA-XT module will take center stage when the next version of Opus Suite is released. By integrating advanced cost models, the updated module will provide even more precise insights into not only the cost of individual repairs but also how different repair decisions influence the overall life cycle costs.