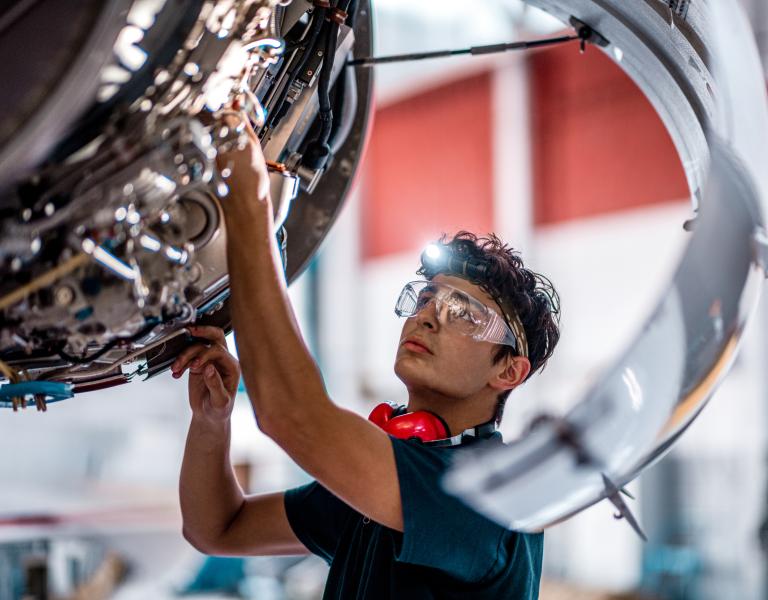
OPUS10 – More than Spare Parts Optimization
To many, OPUS10 – one of the software tools in Opus Suite – is synonymous with cost effective spare parts optimization. With its realistic modeling of technology and support solution, rapid calculations, and results that reduce the spare part investment by 30% or more – while also increasing system availability – OPUS10 has become an industry standard in this field. But as you will find below, it has a lot more to offer.
Spare Parts Optimization
OPUS10 is ideal for finding the most cost effective answer to questions such as:
- What spare parts assortment should I have in stock, and how should I allocate it to the different stock facilities to ensure maximum overall performance at the lowest possible cost?
- A high average performance is great but not enough. I have multiple performance requirements that differ per location and system type. What is then the most cost effective spare parts assortment and allocation?
- How should the spare parts solution be progressively adjusted to ensure cost effective support during a time phased scenario (like a stepwise roll out or phase out of systems)?
- For each component and type of failure, should the component be repaired or discarded when it fails?
- Where is it optimal that repairs occur, locally or centrally?
- What will the spare parts inventory cost given my target performance and support solution restrictions (if such restrictions apply)?
- How will efficiency and costs be affected if e.g. prices, failure rates or lead times increase by X%?
Evaluation of Support Solutions
While spare parts optimization is a core capability and the most common application, OPUS10 provides indispensable decision support in a wide range of situations. It is possible to optimize the entire maintenance concept, to evaluate and comparing alternative support solutions and to make decisions about:
- What is the most cost effective support organization structure?
- Where in the organization should maintenance equipment and personnel be located
- Should all or part of the maintenance be outsourced?
- How many warehouses do I need, and where should they be located?
- What is the most cost effective transport solution?
- How sensitive is my solution to changes or data inaccuracy?
- How should the support organization and spare parts inventory be adjusted during stepwise ramp up or phase-out?
Evaluation of Technical Systems
Another application area is to evaluate different technical systems and find answers to questions such as:
- What system design and configuration are optimal from a supportability perspective?
- Which component choice is the most cost effective from a life cycle perspective, the one with a higher price and better reliability, or the one with a lower price and somewhat lesser quality?
- What component upgrades and design changes are worth the investment because of increased performance and/or reduced cost of ownership?
Modeling and Optimization of Different Scenarios
OPUS10 is scalable and flexible, and can handle smaller scenarios with a handful of components and a few locations to large programs with thousands of components and a complex support solution. The effective optimization algorithms means that even large cases will be optimized in seconds. OPUS10 is capable of accommodating;
- repairable components, discardable / re-ordered items and a combination of these,
- scheduled and unscheduled maintenance,
- time phased scenarios where systems are gradually introduced or phased out
item specific support solutions, - physical or maintenance based product breakdown structures
different criticality levels for components, - multiple optimization requirements per e.g. location, unit or system type.
Read more about application areas
Previous versions release information
Quick tour
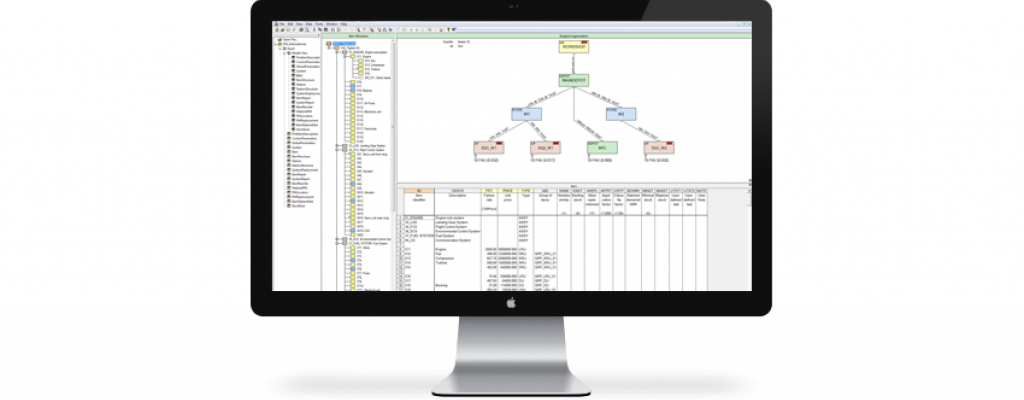
Data Input
The scenario to be analyzed is described in the OPUS10 model, which is based on tables that are used in a flexible way depending on for example complexity and desired level of detail. A “model view” gives the user overview and support when building the model, with a graphic representation of the technical system and its product structure, and the logistic support solution.
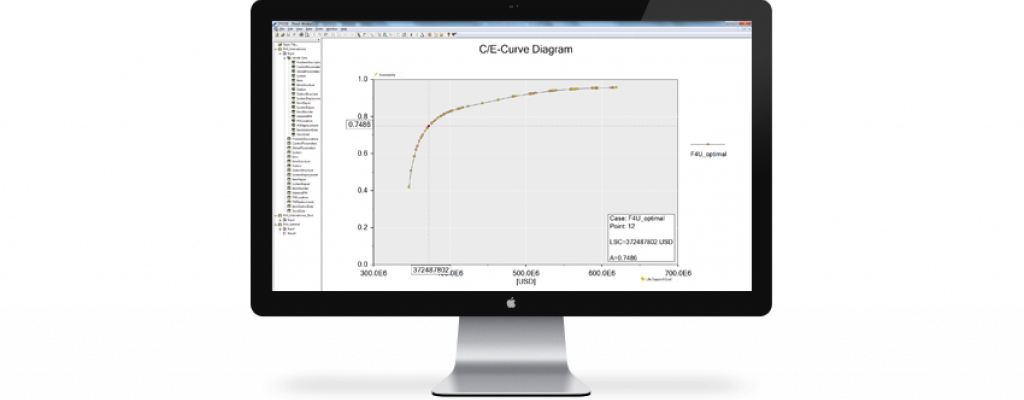
The C/E Curve
The Cost/Efficiency (C/E) Curve is a key step in the OPUS10 optimization. For the described scenario, a series of solution points is generated, showing maximum achievable system efficiency at different budgets. One solution point is selected based on efficiency requirements and/or budget. The optimized solution behind the point can the be examined in the Table view, the Analysis view or in the Reports. By generating C/E curves for different scenarios in the same graph, their cost efficiency can be compared side by side.
Table View
The OPUS10 Results View features an interactive table where you can easily select which solution points, parameters and dimensions to study. For instance, you can list stock levels, investments and service levels per component and location.
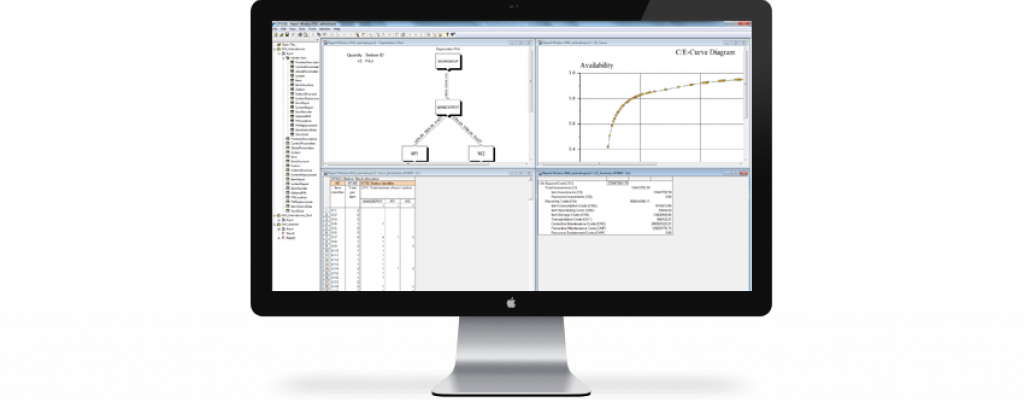
The Report Generator
OPUS10 report generator provides reports that can be customized to show the results that are of interest. There is a great number of result tables and fields to choose from. Reports are easily exported to MS Excel or external databases and ERP systems.
Upcoming courses
Course | Date | Location | |
---|---|---|---|
OPUS10 & SIMLOX Basic Course | Oct 13–17 2025 | Stockholm, Sweden | Learn more |
OPUS10 Extended Course | Oct 15–17 2025 | Stockholm, Sweden | Learn more |
Find out more about the decision support Opus Suite can provide to your organization.
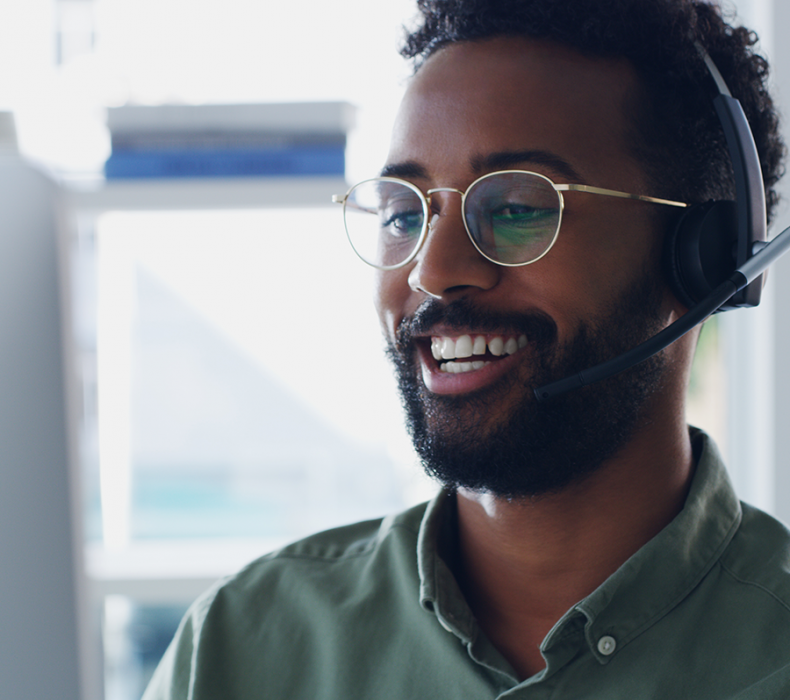